Mail will not be published required. I understand that they probably don't want to or simply can't devote resources to maintaining a free utility, but they should probably put forth a little more effort if they're hoping that that same utility is going to help sell their software. When you save, a temporary file containing the G-code for the generated toolpaths will be created and opened for you. I am always smile when I am researching something and find something by you or one the hammerspace guys. Parting plane is a mold making term for the plane where the two halves of a mold meet up. And here's the finished product:
Uploader: | Vushicage |
Date Added: | 21 April 2006 |
File Size: | 67.38 Mb |
Operating Systems: | Windows NT/2000/XP/2003/2003/7/8/10 MacOS 10/X |
Downloads: | 80894 |
Price: | Free* [*Free Regsitration Required] |
Free CAD as well as free CAM Software! | MecSoft Corporation
Can I change it?? A couple times running through the freeill I got some odd values on this page and the application immediately crashed when I tried to continue even thought the preview looked fine.
Leave a Reply Click here to cancel reply. As a free tool, it's annoying that it's buggy but it's still usable and worth the trouble.
If your part looks like it's about the right size, click next.
FreeMILL – Free Milling Software for programming CNC Mills
There's also a community site for it here: Mail will not be published required. I simply left both offsets to zero since I was going to cut the final part out by hand.
Because of this, its a better strategy currently to learn freeimll set of tools that are available to you, and how to work within their limitations. Here's what the generated toolpaths look like in Mach 3: Since this is an offset, if you have a particular piece you want to cut a model out of, you'll have to measure the piece, look at the reported model size and do some math to get the right offset.
The first step is to load your 3D model. When you save, a temporary file containing the G-code for the generated toolpaths will be created and opened for you.

You can use the same principal to create roughing passes with larger mills then a final detailed path with a smaller mill and smaller stepover distance.
Next you'll select the offset of the stock. Now even if I was interested in purchasing CAM packages, and I am, I don't think freemmill the buggy, poorly maintained at least sincefeature light demo that is FreeMILL would inspire confidence in MecSoft's offerings especially from a hobbyist's perspective, since their tools are not cheap for that demographic. You can see that this thing is actually pretty big the outside edge of the mold is 22".
For instance, rreemill can't specify the maximum depth per pass, so if you've got a design that's relatively thick, the generated toolpaths will have your bit plunging all the way to the maximum Z depth of your part and then dragging free,ill your material. Depending on what you want to do, you may want to simply set this plane to a depth that will get all the details you want to see in the final product as I've done here.
Now we get to select our stepover distance the distance between passes and generate our tool paths.
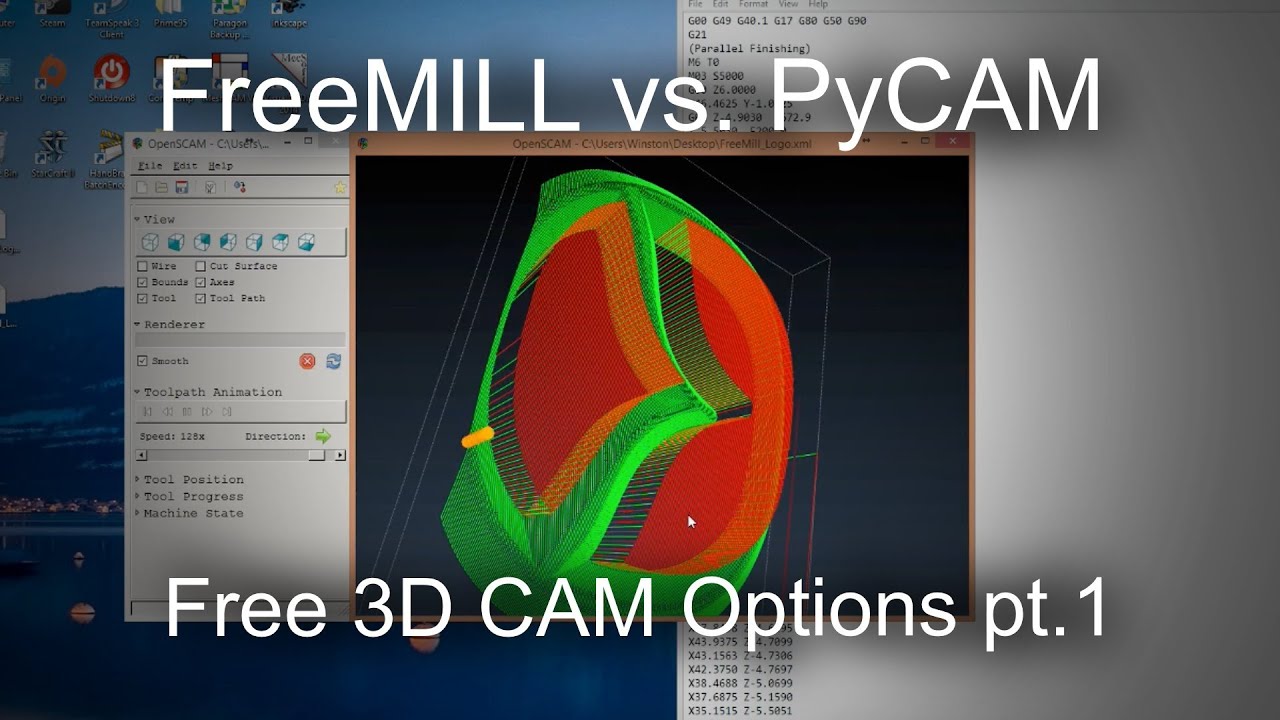
I only used the STL support since it's what my source models treemill in and probably the most widely used format for the hobbyist user and almost all 3D packages support it. Here's some close up shots: More bit options, only flat and corner radius mills are supported ball mills are a special case which are supported, but not V-bits Depth per pass and roughing passes can't be specified Only X or Y parallel finishing available A lot of these shortcomings can be worked through by generating additional passes manually.
If your model is already oriented correctly, just click next, otherwise use the radio buttons to orient it correctly. You can create paths for X parallel finishing and then the Y parallel finishing on your final pass as well.
Download FreeMILL
I assume the default is inches, as this seems to be the standard for models specified in imperial units. I've successfully used dxf2gcode to generate toolpaths that I've run on machines for very simple 2. Next we set up our origin. Here's what it'll look like after the paths have been generated.
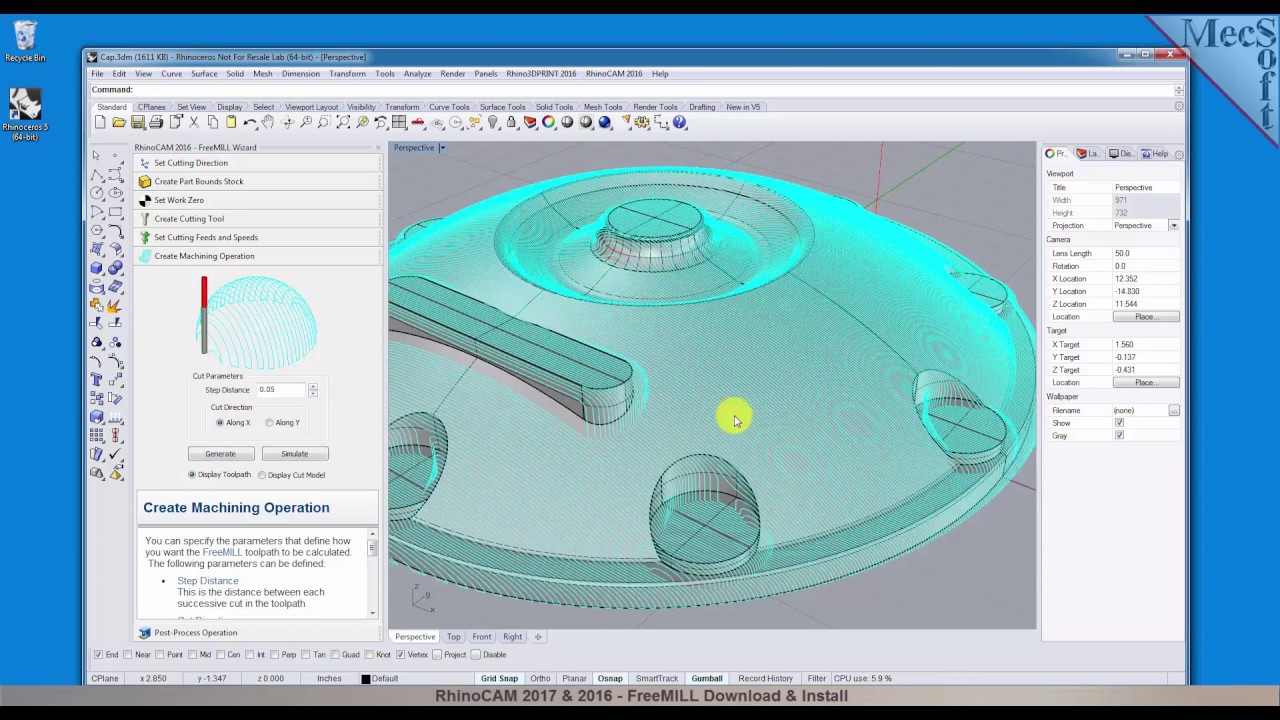
This seems to simply be a way to specify the projection that 3x be cut someone correct me if I'm wrong. Tool path generation seems pretty quick and the progress of the processor is updated in feemill preview window as individual passes are generated.
Next we select the post processor and save our final output. I am always smile when I am researching something and find something by you or one the hammerspace guys. Here's some stuff that would be really nice to have but you can't really do: I'll go into some detail on the games you can play with this setting to achieve various things later.
I'll be keeping an eye frreemill the project and playing with it in more depth in the future.
No comments:
Post a Comment